Shading control with KNX
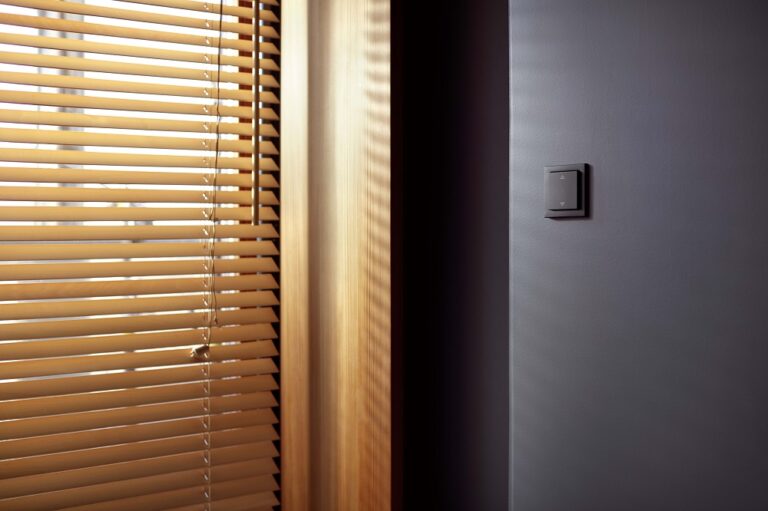
As one of the world's leading building automation solutions for residential and public buildings, KNX system naturally also offers sophisticated solutions for shading control. As there are many different types of shading devices on the market and the way they are controlled varies widely, it is not possible to solve everything with one device. The best way to go is always to use devices developed for the specific task (equipment).
The easiest to control are shutter motors that operate at 230 V and have separate up and down directions. These are the most common motors available on the market. In such cases, it is necessary to use shutter control outputs that can switch 230 V and have a mechanical interlock between the up and down directions. This is necessary to ensure that it is not possible, even accidentally, to output voltage in both directions simultaneously. After all, one of the basic requirements for controls is to protect the integrity of the equipment to be controlled (in this case the shutter motor).
It is also important to note that you should never connect roller shutter motors in parallel! So, either connect the drive of each motor to a separate output, or control the motors in parallel with each other by disconnecting them with relays.
Blinds control actuator
In a KNX shutter control actuator, you can usually set the run-up and run-down times, as well as the lamella switching time. If these are set precisely (individually for each shutter), it is possible to position the shutter motors for simple shutter motors, which otherwise only have up and down directional outlet. This means that if you want to move your shutter to a preset position with a single button press or some kind of trigger, you can do it with a 1 byte value assignment. Of course, this is also true for the slat position (if we have slat blinds). Of course, this requires measuring the running times for each blind individually, so that we can set the desired positions accurately. Up and down times should be measured separately, as the down time for a roller shutter is usually a little less than the up time, because gravity makes the down time shorter. Of course, there may be other cases. Since positioning here depends on accurate measurement of the running times - which admittedly is not entirely exact - it may be useful to set up your actuators so that at certain intervals the shutters automatically take a reference point shot from which the timing is reset. In this case, even if there is minimal slippage in the system, they will not add up - thanks to the regular reference recording.
Limit switch
Although the shutter motors have limit switches, the shutter control actuators can be set to switch off the outputs after a certain time, so that the wires to the motor are not de-energised. In such a case, a new parameter is set to set the runtime values and a slightly longer time for the output to switch off after this time. In this time, it should be safe for the shield to reach from one end position to the other. In almost all these shutter controls, the change of direction time can be set. This is necessary because, in order to increase the life of our shutter motor, we do not apply the voltage in both directions for even a short time at a time, but the user can suddenly start the up direction while the shutter is running in the down direction. A large roller shutter, due to its inertia, will still move downwards for some time (even if we are talking about tenths of a second) if it no longer receives downward voltage. In such cases, it is not advisable to apply the reverse voltage to the motor immediately. Therefore this time can be set as a separate parameter.
There are shading solutions on the market that can be controlled not by 230 V but by, say, 24 V DC. In these cases, the relay output in the 230 V shutter actuators could obviously also switch 24 V DC, but a different solution is still needed. Because in most cases, the change of direction for 24 V DC motors can be solved by reversing the polarity, and this requires actuators that do not simply have normally closed outputs, but solve the polarity reversal themselves.
To complicate matters further, some motors, such as curtain movers in many cases, can be started by a pulse in one direction or the other and stopped by another pulse in the same or the opposite direction. In such cases, it is necessary to choose KNX actuators and controls that are capable of controlling the shutter by pulses.
Use of motors
In cases where SMI motors are used, they can be strung onto an SMI bus, so that SMI control and power is supplied to the motors. The intervention itself (processing of the control signals) is done in the motor, as in this case there is also direct communication between the KNX system and the motor, allowing a much more precise control, but with a more limited choice of available motors.
If you use KNX-compatible motors from the start, the possibilities are almost endless. In such cases, there is a direct link between the motor and the system. It is possible to know exactly what position the motor is in, e.g. whether there is a blockage or other non-operational state.
The construction of the power trail depends on the type of motor (control) and how much selective protection you want to provide, as well as the preparation for any subsequent electrical modifications. If this is possible, the most practical solution is to wire each electric shutter (motor) to be controlled into the distribution box. In this case, all electrical modifications can be easily made in the distribution boxes without having to touch anything in the field, and selective overcurrent protection can also be easily achieved. Occasionally, due to an installation fault, a shutter may become shorted, for example, the motor may wind up the incoming power cable. In such a case, if the individual motors are wired separately into the distribution board, they can be easily disconnected while the shutter installer is working on the fault and it will not cause any disruption to the other circuits.
Manual and automatic operation
Controlling the shading of a modern family home or even a large office building requires a highly sophisticated system. KNX, with its 30 years of history, offers a lot of possibilities to meet the most diverse requirements. It is important to remember that whatever control we are talking about should not be an end in itself, but should facilitate everyday use, while saving energy and ensuring the stable operation of the building for decades.
Classically, in a well-functioning system, there is a synergy between manual operation, automatic control (even by time schedule) and consideration of external or internal parameters. Shutters play a variety of roles in our buildings. These must also be followed by the automation.
Over the past 15-20 years, solar tracking and the use of external weather conditions to control our shading systems has become increasingly important. This means that, depending on the type of shade and its purpose, the control reacts to the outside temperature, wind speed or even the strength and direction of the sun. It may even respond to rainfall. Although the latter is more commonly used for skylights.
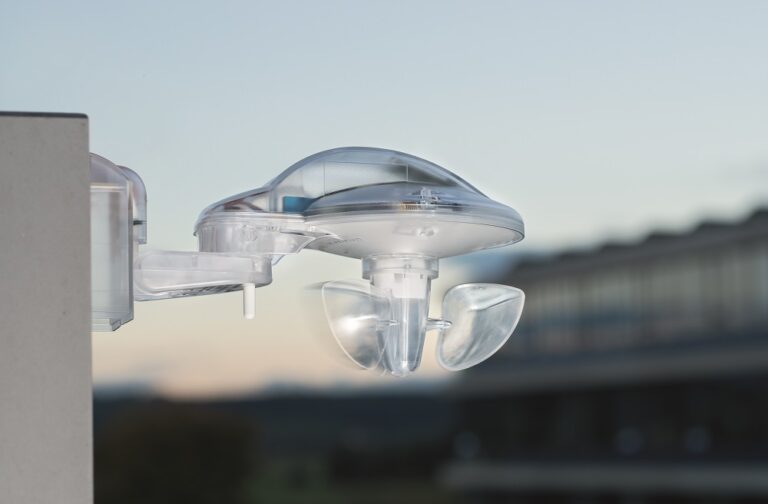
KNX weather station
In a KNX system, you can choose from a wide range of weather stations or devices that detect a single parameter. Figure 1 shows a typical weather station, which is able to detect the current illumination value, wind speed, precipitation and temperature. In modern stations, 3 light sensors have been replaced. The unit should be positioned to face south. It can then measure east, south and west brightness separately. But of course these can also be averaged. Depending on which shade you want to control. Wind speed is typically measured with a wind wheel. There are also wind speed sensors that do not have a mechanical element, so they are not windmills. These measure the air speed electronically. In practice, however, this does not give as accurate a reading as the mechanical version. Therefore, wind wheel sensors are still used today.
There are a number of shades that need to be lowered in case of high winds, for example, to protect the building and windows. In other cases, on the contrary, the shading structure itself must be protected from the harmful effects of the wind. Therefore, the automatic system must be able to assign different functions to different limits. For example, roller shutters are not sensitive to wind. Therefore, they are not usually controlled separately according to wind speed. However, shutters are raised above 50-60 km/h. In the case of arm blinds, however, wind speeds of 30-35 km/h are sufficient for them to be automatically retracted. Sun sails usually have their own built-in sensor.
Although, in principle, in a KNX system, we all strive to have no redundancy. In some cases, however, we recommend it. Just think about why a solar sail has its own wind sensor. In many cases, the use of a weather station in a system is sufficient. But if the building is large enough and the facades are articulated enough to include various shading devices, it is likely that wind sensors will need to be installed in several locations. This is because local wind loads can vary greatly from one part of the building to another. In this case, it is not sufficient to control all the shading devices with sensors placed at one location in the building, because the more sensitive devices must always be controlled according to the wind conditions at that location.
Sun tracking
Speaking of weather station placement, it is important to note that it must be done very carefully. Because of the light sensors, it should always be placed and oriented to the south. A location that is not shaded by the building itself or other buildings and that is not obstructed by surrounding vegetation to ensure correct measurements. This can usually be achieved at a high point on the building. However, care must be taken that this does not take the place of a lightning rod!
For more than a decade, some of the KNX weather stations have been able to control their shading systems according to the position of the sun. This is the classic sun tracking function. For this to work properly, the latitude and longitude of the building's location must be set in the sensor. So the coordinates. Taking these into account, the astro function in the device will tell the system at any given moment at what angle the sun is shining on the building.
However, this is not enough for proper control. The device shown in the figure is able to set up to 8 different facades. So the exact orientation of each facade. After all, this affects the angle at which the sunlight reaches your shaded window. By adjusting these, we can now create a very effective shading system. This not only protects the condition of the equipment, but also provides the best protection from the sun's rays. After all, strong sunlight could cause our rooms to overheat or use too much energy to cool them down. So it's obvious why summer sun tracking is necessary.
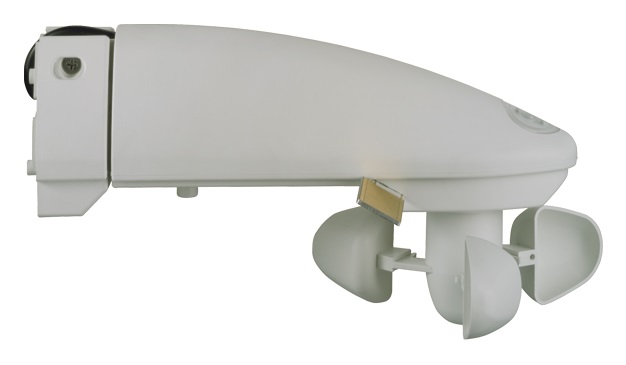
Winter months
But winter brings a different challenge for the system. In winter, we particularly like solar gain to contribute to heating. This quasi reduces the energy demand. Only if the sun is shining, of course. But in our modern buildings, we may need to protect our interiors from overheating even in winter. It sounds strange, but in cases where we have huge windows with very good insulating properties facing south, it is possible that even in winter there will be too much solar gain and solar protection will still need to work. It is therefore important to design the system carefully. Of course, if such a "problem" occurs during operation, it will only mean some adjustment in the case of KNX. It is not necessary to change the design of the system.
e sun tracking function is therefore a very important and almost always used solution. But we must not forget that buildings are inhabited by people who may have needs that sometimes override the automatic system. For example, in a detached house, the sun tracking may mean that the blinds are raised because there is not enough sunshine to justify the blinds being lowered. However, the owner still wants to relax in the afternoon. So he uses the wall-mounted control to lower the blinds and goes to bed. In the meantime, however, the outside sunlight will be so intense that the automatic shutter will lower the blinds. So far, this is not a problem because the blinds are lowered anyway. But when the shutter is raised again, we don't want that in the room. So we need to somehow disable the sun tracking, but only in that room. A lock or automatic off button would be good for this. But if the owner forgets to enable it again, it won't work the next day. That's why we need to use intelligent solutions that can operate the house as required without having to press buttons and solve problems like this.
What you have just read here is only a small part of an intelligent KNX shading control. In practice, there are much more diverse needs, all of which need to be addressed.